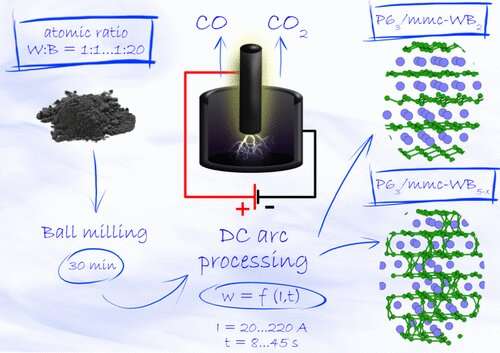
Skoltech researchers and their
colleagues from Tomsk Polytechnic University have proposed an efficient and
inexpensive way to synthesize superhard tungsten boride, used in drilling and
other industrial technologies. The research describing the new technique was
published in the journal Inorganic Chemistry and was featured on the
cover of the May issue.
When they were discovered, tungsten borides captured the imagination of scientists due to their hardness, thermal resistance, low thermal conductivity, and other fascinating mechanical properties superior to those of other materials that had remained unrivaled for almost a century. However, the existing methods of tungsten boride synthesis require either a vacuum or an inert atmosphere under high pressure. This increases production costs and limits scalability and production volume.
"We were looking for an efficient approach to large-scale synthesis of WB5–x, a particular tungsten boride variety that has extremely high wear resistance," says the principal investigator of the study, Assistant Professor Alexander Kvashnin of Skoltech's Project Center for Energy Transition and ESG. "It took us a lot of time and energy, and identifying the distinct phases in the synthesized samples turned out to be a challenge. But computational methods came to the rescue, and after thoroughly investigating the synthesis conditions and the structure of the obtained material, we found that we had succeeded in synthesizing a two-phase sample containing WB2 and WB5–x."
The paper's lead author, Research Scientist Alexander Pak from the Ecoenergy 4.0 Research Center at Tomsk Polytechnic University, comments: "The crystal phases of tungsten boride predicted by our Skoltech colleagues were successfully obtained using the original vacuumless atmospheric arc plasma synthesis technique in the DC arc plasma reactor developed at Tomsk Polytechnic University. By simplifying the method and reactor design, we managed to eliminate a number of costly high-tech components. Compared with immediate analogs, we estimate our method to consume up to 90% less power, at least when synthesizing material in the amounts typical for lab experiments."
The specially built experimental setup used in the study consisted of a graphite cathode in the form of a crucible and a rod-shaped anode that could fit inside, also made of graphite. The initial mixture of powdered tungsten and boron was compacted and placed at the bottom of the crucible. Then an electric arc discharge was initiated between the anode and the cathode in normal air. As a result, atmospheric oxygen reacted with the carbon in graphite, producing a self-contained gas environment in the crucible. As the electric arc drove the temperature up, synthesis occurred, yielding different tungsten borides in a proportion determined by the source materials ratio and plasma treatment parameters. Importantly, this whole process does not require a vacuum environment, making the method applicable to large-scale industrial production.
"We also improved the method to allow for fine-tuning of the experimental parameters to control product composition," Kvashnin adds. "This enabled the proportion of the desirable WB5–x phase in the sample to be increased to 61.5% by volume."
The new vacuumless technique is the first step toward controllable inexpensive large-scale synthesis of superhard tungsten boride with exceptional mechanical properties for a wide range of industrial applications. According to the researchers the material will even be fit to scrub carbon dioxide from factory emissions and produce blue hydrogen. The main advantage of using WB5–x as a catalyst in that process is its capacity to be reused.