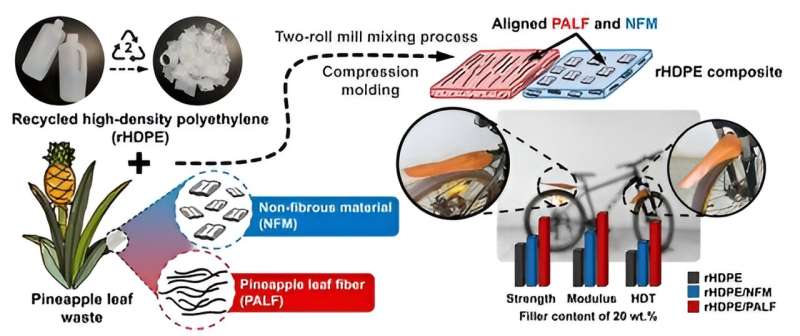
Researchers
from Thailand have pioneered the conversion of waste HDPE milk bottles into
high-stiffness composites, using PALF reinforcement for a 162% increase in
flexural strength and 204% in modulus. This eco-friendly upcycling boosts
mechanical properties while sequestering carbon, presenting a promising path
for sustainable materials.
To meet the UN Sustainable Development Goals by reducing the making of new plastic materials and making use of natural fiber from agriwaste, this research addresses the potential of repurposing high-density polyethylene (HDPE) milk bottles. The aim is to create high-stiffness, high-heat-distortion-temperature (HDT) composites through upcycling.
The composite matrix utilizes recycled high-density polyethylene (rHDPE) obtained from used milk bottles, while the reinforcing fillers are derived from waste pineapple leaves, encompassing both fibers (PALF) and non-fibrous materials (NFM). The research is published in the journal Polymers.
To prepare these composites, a two-roll mixer is employed to blend rHDPE with NFM and PALF, ensuring optimal alignment of the fillers in the resulting prepreg. Subsequently, the prepreg is layered and compressed into composite sheets. The incorporation of PALF as a reinforcing filler plays a pivotal role in significantly enhancing the flexural strength and modulus of the rHDPE composite.
A particularly noteworthy result is observed with a 20 wt.% PALF content, leading to an impressive 162% increase in flexural strength and a remarkable 204% increase in modulus compared to pristine rHDPE.
While the rHDPE/NFM composite also exhibits improved mechanical properties, albeit to a lesser extent than fiber reinforcement, both composites experience a slight reduction in impact resistance. Notably, the addition of NFM or PALF substantially raises the heat distortion temperature (HDT), elevating the HDT values to approximately 84°C and 108°C for the rHDPE/NFM and rHDPE/PALF composites, respectively. This is in stark contrast to the 71°C HDT of neat rHDPE.
Furthermore, the overall properties of both composites are further enhanced by enhancing their compatibility through the use of maleic anhydride-modified polyethylene (MAPE). Examination of impact fracture surfaces on both composites reveals heightened compatibility and clear alignment of NFM and PALF fillers, highlighting the improved performance and environmental friendliness of composites produced from recycled plastics reinforced with pineapple leaf waste fillers.
Improved mechanical properties, especially resistance to deformation under normal or high temperatures, enhance the feasibility of using the product with reduced weight or a thinner design. This is crucial for applications like automotive parts.
This research underscores the promising avenue of utilizing waste materials for sustainable composite development, contributing to the broader goal of reducing environmental impact in the plastics industry. It also contributes to carbon removal by sequestrating carbon in durable products.
Associate Professor Kheng Lim Goh, technical advisor of the PALF-HDPE study, considers the upcycling of HDPE milk bottles with pineapple leaf fibers a significant advancement. He is excited that this approach transforms abundant waste into high-stiffness HDPE composite materials with enhanced mechanical properties, holding promise for various industries, including biomedical and automotive.
However, to maintain a sustainable PALF supply chain for high-stiffness HDPE production that can be applied at speed and scale, pineapple farmers must prepare for and adapt to climate change effects, including erratic rainfall, temperature extremes, drought, soil erosion, invasive weeds, and durable pests.
Both farmers and crop scientists should utilize information from climate projections, crop and economic models, and empirical field data to identify how pineapple crops can withstand dryness and inadequate soil moisture. They also need to explore alternative options for sustaining pineapple production to ensure a consistent PALF supply for high-stiffness HDPE composite material manufacturing.