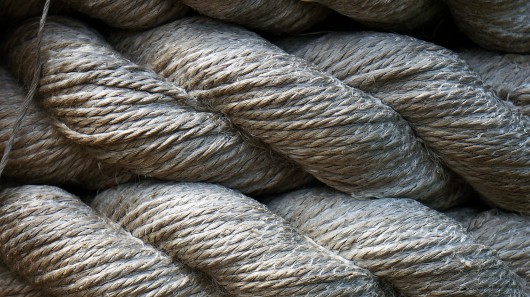
Using waste hemp fibers as the starting material, researchers at the University of Alberta in Canada have developed a high-performance electrode material for supercapacitors at one thousandth the cost of the more commonly used graphene. The advance could lead to supercapacitors that are both cheaper and able to operate under harsh environmental conditions.
Despite a bad reputation, hemp is a truly remarkable plant. It can be grown on the cheap, requiring very little care even in very cold and dry environments, and has many uses, ranging from construction material to clothing, bioplastics, and even biofuel creation.
In what may be the most surprising application of the lot, a team led by Prof. David Mitlin was able to build supercapacitor electrodes from the inner bark fibers of (THC-free) hemp, a waste product. Remarkably, the performance of the device was on par or better than standard graphene-based supercapacitors, even though the new material can be obtained at one thousandth of the cost and processed with ease.
Hemp inner bark fibers, or "bast fibers," are similar to yarn in their outward appearance; however, when looked at under the microscope, they reveal themselves as a remarkable nanoscale composite consisting of semicellulose, lignin and crystalline cellulose. The latter makes up around 70 percent of the material by weight, and is the component of interest to the researchers, as it can be processed to obtain graphene-like carbon nanosheets.
After realizing that the material had a fairly unique structure, Mitlin and colleagues were able to develop a very simple, inexpensive and scalable way to produce carbon nanosheets from them. The researchers first heated the fibers for 24 hours at around 350° F (180° C) – essentially, pressure-cooking them in water – to dissolve the semicellulose and lignin components; they then exposed the resulting material to potassium hydroxide to create graphene-like carbon nanosheets.
The resulting sheets are far from perfect, as they are crumpled and riddled with holes. But as it turns out, when it comes to building supercapacitor electrodes, this is a very good thing.
In order to build high-efficiency capacitors, the surface area of the electrode must be as high as possible, so that electrically charged ions can access the material easily and transport charge effectively.
In its purest form, graphene is a very flat, one-atom thick sheet of carbon atoms. Because they are so flat, when laid out next to each other on a flat surface, the sheets tend to stack on top of each other rather easily. This decreases the surface area of the electrode and, consequently, also the performance of the device over time.
The hemp-derived nanosheets, on the other hand, already come pre-crumpled (so they won't tend to stack on top of each other quite as much) and holey (which increases the surface area accessible by ions). The sheets, 10 to 30 nanometers thick, are also highly electrically conductive, which is essential for supercapacitors. Although they aren't quite as conductive as graphite, Mitlin says they are 10 times more conductive than state of the art activated carbon.
The supercapacitors built using the nanosheets performed remarkably well, yielding energy densities up to 12 Wh/kg, about three times higher than commercial counterparts, and power densities over 100 times higher than conventional Li-ion batteries. Unlike other supercapacitors, the device also can also operate under wider temperature margins, from 0 to 100° C (32 to 212° F). However, the most surprising metric is the cost of the material as compared with normal graphene.
"Our material is very graphene-like in its performance, but cost-wise it's about one thousand times cheaper," says Mitlin. "As far as manufacturing, we did the cost analysis and it's anywhere between $500 and $1,000 a tonne."
Mitlin is now gearing up production for small-scale manufacturing in the US.