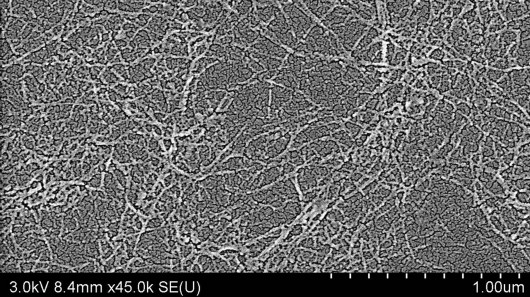
While we hear a lot about the wonders of materials like graphene and carbon nanotubes, nanofibrillated cellulose (aka: Cellulose NanoFibrils, or CNF) also shows a lot of promise. A type of "nanocellulose", it can be used to produce composite materials that are strong, light, electrically-conductive and oxygen-impervious. Additionally, it uses an existing waste product as its feedstock. Unfortunately its production process is fairly energy-intensive, limiting its widespread use. Thanks to a new technique, however, that may soon no longer be the case.
CNF is currently made by adding water to cellulose-containing materials (usually wood waste, as would be found at paper or lumber mills), then using high-pressure homogenizers, grinders or microfluidizers to rip the wood fibers into much smaller cellulose nanofibers. This results in a gel which is subsequently freeze-dried to remove the water, leaving the long, interconnected nanofibers behind.
Those nanofibers are then added to other materials, to produce items such as oil-spill-absorbing sponges and eco-friendly plastic automotive body panels. CNF could also conceivably be used in things like bio-compatible/ bio-absorbable wound dressings, touchscreens, and food packaging.
The amount of energy required to rip the wood fibers apart is considerable, however. It's possible to weaken the wood's molecular structure by pretreating it, thus greatly lessening the amount of "ripping" energy required, although the pretreatment process (in some cases) requires expensive chemicals that end up in leftover waste water.
Scientists from Edinburgh Napier University and pulp/paper producer Sappi claim to have addressed these problems, with their proprietary new process.
"What is significant about our process is the use of unique chemistry which has allowed us to very easily break down the wood pulp fibers into nanocellulose," said the university's Prof. Rob English, who led the research along with Dr. Rhodri Williams. "There is no expensive chemistry required and, most significantly, the chemicals used can be easily recycled and reused without generating large quantities of waste water."
Sappi is now planning on building a pilot plant for production of the material, which ought to be up and running towards the end of next year. The CNF produced there should be easier to mix with other materials than is currently possible, plus it can be made in either hydrophobic or hydrophilic (water-repelling or -absorbing) versions, for different applications.
Scientists at the University of Texas at Austin are developing a different process, in which algae is converted into nanocellulose.