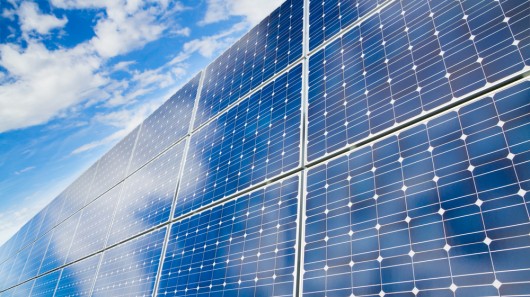
Brown University researchers have developed a new method for making solar cells from perovskite. Unlike existing techniques, the new method doesn't require the application of heat, and can produce highly efficient, thinner versions of the light-absorbing films.
The use of perovskites – a class of crystalline material – in solar cells is an area of increasing interest. The films exhibit excellent light absorption properties and are significantly cheaper to produce than the silicon wafers used in standard energy cells.
The efficiency of perovskite cells has improved significantly over the years since they were first introduced in 2009, increasing in efficiency from just four percent up to a much healthier 20 percent today. While that's still shy of the 25 percent efficiency of silicon wafer-based cells, it's believed that continued development and commercialization will improve those numbers looking forward.
Existing techniques for making perovskite cells involve the application of heat. Precursor chemicals are dissolved into a solution and applied to a substrate, with heat then used to remove that solution, leaving perovskite crystals in a film across said substrate.
Techniques that rely on the application of heat have, in the past, allowed for the production of films measuring fractions of a centimeter in diameter. To do so, the solution has to be exposed to temperatures of between 100 and 1500C (212 to 3020F), and the process can lead to uneven crystal formation, which in turn creates small pinholes in the resulting film that lower efficiency.
To tackle the issues with heat-based perovskite cell production, the researchers came up with a new method, known as solvent-solvent extraction (SSE).
The method involves dissolving the perovskite precursors in a solvent called NMP, then coating it onto a substrate – just the same as existing techniques. However, rather than applying heat to the substrate, it's instead bathed in a second solvent known as diethyl ether (DDE), which removes the NMP solvent from the mix. This allows crystals to form evenly over the substrate, creating an ultra-smooth film.
Whereas heat-based methods take a minimum of one hour to complete, SSE takes just two minutes, and can produce much thinner films without the appearance of pinholes – just 20 nanometers, compared to around 300 nanometers produced by existing techniques.
The cells can also be made larger than with existing methods – up to several centimeters square – and as no heating is involved, the crystals can be formed on almost any substrate, including heat-sensitive polymers.
The ability to make thinner cells may also have other benefits. Whereas thicker perovskite cells are opaque, SSE-produced cells are thin enough to be partially transparent and could therefore be used in windows, and the process could even be tweaked to produced colored cells.
"These could potentially be used for decorative, building-integrated windows that can make power," says Nitin Padture, professor of engineering and director of the Institute for Molecular and Nanoscale Innovation.
The team intends to continue its research, collaborating with scientists at the National Renewable Energy Laboratory in Colorado. The study was published in the Journal of Materials Chemistry A.